- January 22, 2025
- Posted by: wellcoindustries
- Category: Rebar
Introduction
Fiber Reinforced Polymer (FRP) reinforced rebar is redefining how we approach concrete reinforcement. As modern construction projects aim for longer-lasting, more resilient structures, the demand for advanced materials like FRP is skyrocketing. In this article, we explore the core advantages of FRP reinforced rebar, why it matters for today’s builders, and how you can effectively integrate it into your projects.
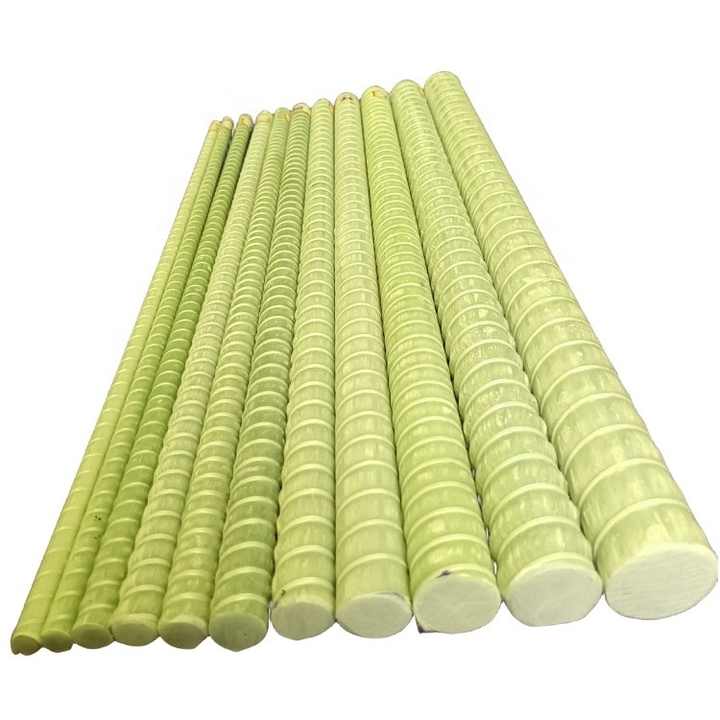
Understanding FRP Reinforced Rebar
FRP reinforced rebar is produced by combining high-strength fibers—such as glass (GFRP), carbon (CFRP), or basalt (BFRP)—with a polymer resin. This fusion results in a highly resilient, lightweight reinforcement bar designed to replace or supplement traditional steel rebar. While steel has long been the go-to material, engineers are now embracing FRP solutions to combat challenges like corrosion, high maintenance costs, and limitations in structural durability.
FRP is often misunderstood as a product solely for specialized industries, but recent advancements and increased affordability have made it a practical choice across a wide range of construction applications. According to the American Concrete Institute (ACI), FRP bars can extend the life of concrete structures, particularly in harsh or corrosive environments. By using FRP, builders can reduce future repair and rehabilitation costs while maintaining robust structural integrity.
5 Essential Benefits of FRP Reinforced Rebar
Corrosion Resistance
One of the most significant challenges with steel rebar is corrosion—especially in climates with high humidity, saltwater, or chemical exposure. Over time, steel can rust, expand, and compromise the structural integrity of concrete. FRP reinforced rebar, on the other hand, doesn’t corrode. It maintains its form and strength even in aggressive conditions, making it an ideal choice for bridges, marine structures, and industrial facilities where corrosion is a constant threat. By opting for corrosion-resistant FRP, construction projects can reduce maintenance needs and extend service life by decades.
Lightweight Yet Strong
FRP reinforced rebar is considerably lighter than steel—up to 75% lighter in some cases. This reduced weight results in easier handling on-site, lower transportation costs, and faster installation times. Contractors often appreciate how this can reduce labor intensity and the risk of on-the-job injuries. Despite being lightweight, FRP rebar does not compromise on strength. Many FRP variants can match or even exceed the load-bearing capabilities of traditional steel in tensile strength tests.
High Tensile Strength
Tensile strength refers to how much pulling force a material can withstand before failing. FRP reinforced rebar can possess a tensile strength several times higher than that of steel. This high tensile capacity allows designers greater flexibility in creating innovative structural solutions that were previously not feasible with steel. From slender architectural elements to cantilevered structures, FRP’s impressive tensile performance broadens the horizons of modern engineering.
Non-Conductive Properties
Unlike steel, which conducts electricity and heat, FRP reinforced rebar is non-conductive. This property makes it especially valuable in structures where electromagnetic fields or stray currents pose a risk—such as electrical substations, medical facilities with sensitive imaging equipment, and areas prone to lightning strikes. Incorporating non-conductive reinforcement bars helps maintain stable electrical environments, reducing potential hazards and improving overall safety.
Enhanced Durability
Durability isn’t limited to corrosion resistance alone. FRP reinforced rebar also boasts excellent fatigue strength, reduced creep, and high resistance to chemical degradation. In projects exposed to deicing salts, acidic soil, or alkaline conditions, FRP remains stable and maintains long-term performance. Its consistent structural integrity means fewer repairs, less downtime, and a predictable lifecycle for building owners and facility managers.
Practical Applications in Modern Construction
FRP reinforced rebar is no longer confined to niche applications. From water treatment plants to multi-story commercial buildings, the use of FRP is becoming increasingly common. In coastal regions, for example, bridge decks and piers benefit from FRP’s immunity to salt-induced corrosion. Tunnels, parking garages, and retaining walls in humid environments also gain extended lifespans by eliminating the corrosion factor. Additionally, the push toward sustainable building practices aligns well with FRP’s low lifecycle maintenance requirements, minimizing resource consumption and environmental impact over time.
A Quick Guide to Specifying and Installing FRP Reinforced Rebar
- Determine Project Requirements
- Evaluate the environment (coastal, chemical exposure, temperature extremes).
- Consider your design codes (ACI, CSA, local guidelines) for FRP use.
- Identify the loads, bending moments, and specific durability needs.
- Choose the Right Type of FRP
- GFRP (Glass Fiber Reinforced Polymer) is often cost-effective and suitable for most general construction.
- CFRP (Carbon Fiber Reinforced Polymer) offers higher strength but at a premium cost.
- BFRP (Basalt Fiber Reinforced Polymer) provides a balance of performance and durability.
- Coordinate with Suppliers
- Work with reputable suppliers experienced in FRP solutions.
- Request samples and detailed product specifications.
- Check that certifications and test data align with your project standards.
- Plan for Installation
- Ensure crews receive proper training on handling and cutting FRP bars.
- Double-check rebar placement guidelines to maintain clear spacing.
- Use specialized cutting tools (e.g., diamond blades) to avoid bar damage.
- Secure and Inspect
- Tie or secure bars using recommended fasteners or ties that won’t compromise the FRP surface.
- Conduct regular inspections throughout the pour to maintain positioning.
- Document every step to ensure quality control and compliance with design specifications.
Following these guidelines helps you leverage the full performance benefits of FRP reinforced rebar while avoiding installation pitfalls. Proper planning and communication between designers, engineers, and contractors can significantly reduce the learning curve.
Conclusion
FRP reinforced rebar is quickly becoming a cornerstone in modern construction thanks to its durability, corrosion resistance, lightweight nature, and high tensile strength. By considering its unique properties and integrating it thoughtfully into your next project, you can reduce maintenance costs, enhance long-term performance, and help shape more resilient infrastructure.
Are you ready to explore FRP reinforced rebar for your upcoming construction project? Share your thoughts or questions in the comments below. If you found this article helpful, spread the word on social media or subscribe to our newsletter for more insights on innovative building materials and practices. Your feedback drives our continued commitment to delivering reliable, actionable content for the construction industry.