- July 24, 2024
- Posted by: wellcoindustries
- Category: Rebar
Introduction
In the ever-evolving construction industry, materials that offer durability, efficiency, and cost-effectiveness are always in high demand. One such innovation that is rapidly gaining traction is the use of fiberglass rebar couplers. These couplers provide a robust alternative to traditional steel rebar couplers, offering a range of benefits that make them ideal for various applications. In this article, we will delve into the world of fiberglass rebar couplers, exploring their advantages, applications, and the installation process to help you understand why they are becoming a preferred choice in modern construction projects.
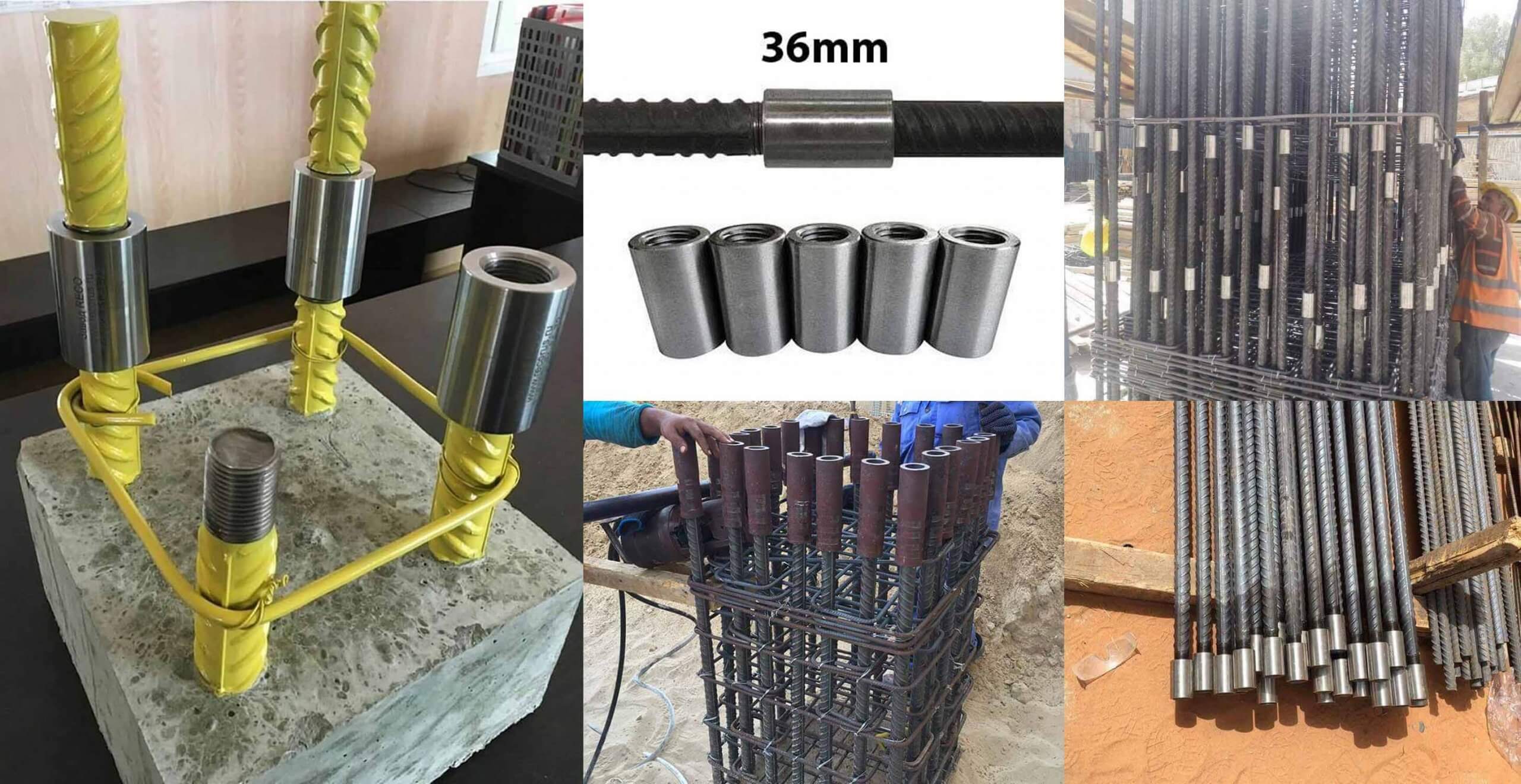
What are Fiberglass Rebar Couplers?
Fiberglass rebar couplers are connectors used to join fiberglass rebar, a type of reinforcing bar made from glass fiber reinforced polymer (GFRP). Unlike traditional steel rebar, fiberglass rebar is non-corrosive and lightweight, making it a superior choice for specific applications. These couplers ensure that the rebar remains aligned and maintains its structural integrity, providing strength and stability to the construction.
- Material Composition: Fiberglass rebar couplers are typically made from high-strength fibers embedded in a resin matrix, offering durability and flexibility.
- Types of Couplers: There are various types of fiberglass rebar couplers, including threaded, adhesive, and mechanical couplers, each designed for specific applications and installation methods.
Benefits of Fiberglass Rebar Couplers
- Corrosion Resistance: One of the most significant advantages of fiberglass rebar couplers is their resistance to corrosion. Unlike steel, fiberglass does not rust, making it ideal for use in harsh environments, such as marine or chemical plants.
- Extended Lifespan: The corrosion resistance extends the lifespan of structures, reducing the need for costly repairs and replacements.
- Lightweight: Fiberglass rebar couplers are significantly lighter than their steel counterparts, reducing transportation costs and making handling easier on-site.
- Ease of Installation: The lightweight nature simplifies the installation process, reducing labor costs and time.
- High Tensile Strength: Despite being lightweight, fiberglass rebar has a high tensile strength, offering robust support for various construction needs.
- Structural Integrity: Maintains structural integrity under heavy loads and stresses.
- Non-conductive Properties: Fiberglass is non-conductive, making it a safe choice for structures that need to avoid electrical conductivity.
- Safety in Electrical Environments: Ideal for use in environments where electrical insulation is crucial.
Applications of Fiberglass Rebar Couplers
Fiberglass rebar couplers are versatile and can be used in various applications:
- Infrastructure Projects: Ideal for bridges, tunnels, and highways where longevity and durability are crucial.
- Enhanced Durability: Reduces maintenance costs and enhances the lifespan of infrastructure projects.
- Marine Construction: Perfect for docks, seawalls, and other marine structures due to their resistance to saltwater corrosion.
- Resistance to Saltwater: Ensures longevity and stability in marine environments.
- Chemical Plants: Suitable for environments exposed to harsh chemicals, as fiberglass is resistant to chemical reactions.
- Chemical Resistance: Prevents degradation in chemically aggressive environments.
- Other Applications: Includes residential and commercial buildings where reducing maintenance costs is a priority.
- Cost-Effectiveness: Provides long-term savings through reduced maintenance and replacement costs.
Installation Guide for Fiberglass Rebar Couplers
Installing fiberglass rebar couplers involves a straightforward process:
- Preparation: Ensure all materials and tools are ready.
- Checklist: Verify that all required tools, couplers, and safety equipment are available.
- Cutting Rebar: Measure and cut the fiberglass rebar to the required length.
- Precision Cutting: Use appropriate tools to ensure clean and accurate cuts.
- Positioning Couplers: Place the couplers at the ends of the rebar pieces to be joined.
- Alignment: Ensure proper alignment for optimal structural integrity.
- Securing Couplers: Use appropriate adhesive or mechanical fasteners to secure the couplers in place.
- Securing Methods: Choose the correct securing method based on the type of coupler and application requirements.
- Final Check: Inspect the installation to ensure alignment and stability.
- Quality Assurance: Conduct a thorough inspection to verify the installation quality.
Cost and Economic Impact
While the initial cost of fiberglass rebar couplers may be higher than steel, the long-term economic benefits are substantial. The reduced need for maintenance and replacement, combined with the longevity of fiberglass, results in significant cost savings over time. Additionally, the lightweight nature of fiberglass reduces transportation and labor costs, further enhancing its economic appeal.
- Initial Investment: Although the upfront cost is higher, the return on investment is significant due to reduced long-term expenses.
- Maintenance Savings: The durability and resistance to corrosion of fiberglass rebar couplers lead to lower maintenance costs.
- Transportation and Labor: The lightweight nature of fiberglass rebar reduces transportation and labor costs, making it an economically viable option.
Conclusion
Fiberglass rebar couplers represent a significant advancement in construction materials, offering numerous benefits over traditional steel rebar couplers. Their corrosion resistance, lightweight nature, and high tensile strength make them an excellent choice for various applications, from infrastructure projects to marine construction. By understanding their advantages and proper installation techniques, construction professionals can leverage these innovative couplers to enhance the durability and efficiency of their projects. For more information or to explore purchasing options, contact a trusted supplier today.