- October 16, 2024
- Posted by: wellcoindustries
- Category: Rebar
Introduction
In the ever-evolving construction industry, the choice of materials plays a pivotal role in determining the longevity and performance of structures. One material that has gained significant attention is fiberglass rebar, a corrosion-resistant alternative to traditional steel rebar. While steel has long been the industry standard for reinforcing concrete, fiberglass rebar offers unique advantages, particularly when it comes to tensile strength, making it an ideal choice for modern construction projects.
Tensile strength refers to the maximum stress a material can withstand while being stretched or pulled before breaking. In construction, where reinforcing materials are critical to the integrity of a structure, understanding tensile strength is essential. This article delves into the tensile strength of fiberglass rebar, explaining its significance, advantages, testing methods, and applications in the construction industry.
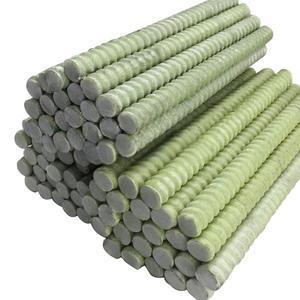
What is Fiberglass Rebar?
Fiberglass rebar, also known as Glass Fiber Reinforced Polymer (GFRP) rebar, is a composite material made from a polymer matrix reinforced with glass fibers. Unlike traditional steel rebar, fiberglass rebar does not rust, making it particularly useful in environments where corrosion is a major concern, such as marine structures, bridges, and parking garages.
Fiberglass rebar is lightweight, easy to handle, and non-conductive, which adds to its growing popularity in construction. It offers a solution for infrastructure that must endure harsh environmental conditions while maintaining its structural integrity. Its primary distinction from steel rebar lies in its non-corrosive nature, but one of the key factors that make fiberglass rebar stand out is its tensile strength, which directly impacts its performance in reinforcing concrete.
The Importance of Tensile Strength in Rebar
Tensile strength is one of the most critical properties of any reinforcing material. In the context of rebar, it measures the ability of the material to withstand forces that attempt to pull it apart. Rebar with high tensile strength ensures that a structure can handle stress and load without deforming or breaking, contributing to the overall durability and safety of the construction.
When comparing fiberglass rebar to steel rebar, one of the key differences lies in their tensile strength. While steel rebar has been the go-to material for its strength and reliability, fiberglass rebar provides comparable tensile strength with additional benefits such as being lighter and resistant to corrosion. For instance, high-quality fiberglass rebar can offer tensile strength values between 60,000 and 120,000 psi (pounds per square inch), which is sufficient for many construction applications, especially where corrosion resistance is prioritized.
The tensile strength of fiberglass rebar contributes to the overall longevity of structures, particularly in environments where steel would degrade over time. This makes it a valuable option for infrastructure projects that require minimal maintenance and long-term durability.
Advantages of Fiberglass Rebar Tensile Strength in Construction
Fiberglass rebar offers several advantages due to its high tensile strength, making it a favorable alternative to steel rebar in many scenarios. Here are some of the key benefits:
- Corrosion Resistance: Unlike steel, fiberglass rebar does not corrode, making it ideal for use in marine environments, wastewater treatment plants, and areas with high moisture or salt exposure. The tensile strength of fiberglass rebar remains unaffected by rust, ensuring the structure’s integrity over time.
- Lightweight: Fiberglass rebar is significantly lighter than steel, which makes it easier to transport and handle on construction sites. Despite its lighter weight, it still maintains excellent tensile strength, ensuring that it performs effectively in high-stress situations.
- Non-Magnetic and Non-Conductive: For structures where electromagnetic interference or electrical conductivity is a concern (such as hospitals or power plants), fiberglass rebar offers an ideal solution without sacrificing tensile strength.
- Longevity and Low Maintenance: The tensile strength of fiberglass rebar, combined with its resistance to corrosion, results in a longer lifespan for structures. This reduces the need for frequent repairs or replacements, leading to lower long-term maintenance costs.
These advantages underscore why fiberglass rebar, with its high tensile strength, is increasingly being adopted in various construction projects, especially those exposed to challenging environmental conditions.
How Fiberglass Rebar Tensile Strength is Tested
Testing the tensile strength of fiberglass rebar is essential to ensure its suitability for different construction applications. Manufacturers and engineers use standardized testing methods to determine the maximum stress the rebar can endure before breaking. These tests follow industry standards, such as the ASTM D7205 (Standard Test Method for Tensile Properties of Fiber Reinforced Polymer Matrix Composite Bars), to ensure consistency and reliability.
The tensile strength of fiberglass rebar is tested by applying a controlled force to a sample bar until it breaks. This provides valuable data on its performance under load. Factors such as the quality of the raw materials, manufacturing processes, and curing conditions can all influence the tensile strength results. For example, improper curing can lead to micro-cracks in the rebar, reducing its tensile strength and overall effectiveness in reinforcing concrete.
Additionally, environmental factors like temperature and exposure to chemicals are also considered when testing fiberglass rebar. Since fiberglass is often used in corrosive environments, it is essential to ensure that its tensile strength remains consistent under different conditions.
Applications of Fiberglass Rebar with High Tensile Strength
Due to its high tensile strength, fiberglass rebar is used in a variety of construction projects, particularly where durability and corrosion resistance are essential. Some common applications include:
- Bridges and Highways: Fiberglass rebar is frequently used in bridge decks and highway construction, where exposure to salt and moisture can cause steel to corrode rapidly. Its tensile strength ensures that these structures can handle heavy loads while remaining intact over time.
- Marine Structures: In marine environments, such as docks, piers, and seawalls, fiberglass rebar’s resistance to corrosion, combined with its tensile strength, makes it an ideal material for withstanding the harsh effects of saltwater.
- Tunnels and Underground Structures: For underground applications where moisture and chemicals are prevalent, fiberglass rebar provides a non-corrosive alternative with excellent tensile strength to maintain the structural integrity of tunnels, subway systems, and sewage systems.
By utilizing fiberglass rebar in these high-stress environments, engineers can ensure that the structures not only last longer but also require fewer repairs over their lifespan, reducing overall maintenance costs.
Conclusion and Call to Action
In conclusion, fiberglass rebar tensile strength is a crucial factor in its growing popularity as a reinforcement material in modern construction. With its impressive resistance to corrosion, lightweight properties, and comparable tensile strength to steel, fiberglass rebar offers a reliable and durable solution for projects in demanding environments. Its use in infrastructure such as bridges, marine structures, and highways showcases its ability to enhance structural integrity while minimizing long-term maintenance costs.
For construction professionals looking to optimize their projects with materials that offer both strength and longevity, fiberglass rebar is a forward-thinking choice. If you’re considering incorporating fiberglass rebar into your next construction project, explore reputable suppliers that offer high-quality products and testing certifications to ensure you’re making the best investment for the future of your infrastructure.