- April 16, 2025
- Posted by: wellcoindustries
- Category: Rebar
Rebar, short for reinforcing bar, is an essential component in modern construction, enhancing the strength and durability of concrete structures. Understanding the chemical composition of rebar is crucial because it directly influences performance, structural integrity, and longevity. By selecting rebar with the right chemical properties, engineers can prevent structural failures, control costs, and optimize safety. This comprehensive guide will explain what rebar is made of, why its chemical makeup matters, and how different elements affect its performance.
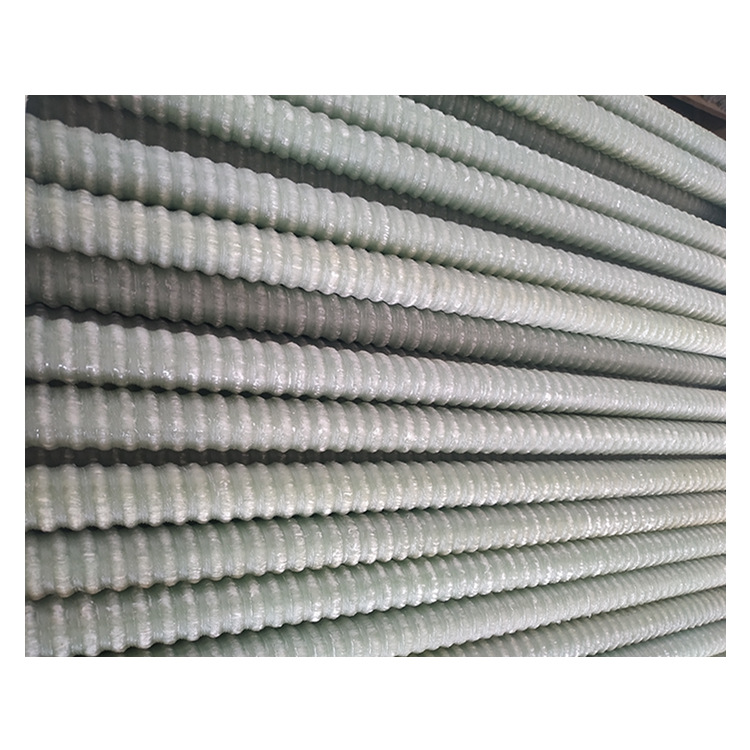
What Is Rebar and Why Is Chemical Composition Important?
Rebar is a steel bar or mesh used to reinforce concrete, increasing its tensile strength. Concrete alone is excellent at withstanding compressive stress but weak in tension. Rebar compensates for this weakness.
The chemical composition of rebar significantly impacts:
-
Strength and durability
-
Resistance to corrosion
-
Weldability and formability
-
Cost-effectiveness
Engineers and builders must carefully consider rebar chemistry to meet specific construction requirements and safety regulations.
Key Elements in the Chemical Composition of Rebar
Several elements influence the quality and performance of rebar. Below are the primary components and their typical effects:
Carbon (C)
Carbon is a critical element influencing the hardness and tensile strength of rebar. Generally:
-
Lower carbon content (around 0.05–0.25%): Enhanced ductility and weldability.
-
Higher carbon content (up to 0.30%): Increased strength but reduced ductility, making rebar less flexible and harder to weld.
Typical composition: 0.20–0.30% for common reinforcement bars.
Manganese (Mn)
Manganese improves hardness, strength, and workability:
-
Acts as a deoxidizer to reduce brittleness.
-
Enhances the tensile strength and hardenability.
Typical composition: 0.60–1.00%.
Silicon (Si)
Silicon is another important deoxidizer that influences the manufacturing quality of rebar:
-
Improves fluidity during production, making steel easier to shape.
-
Helps in creating a cleaner and more uniform final product.
Typical composition: 0.15–0.30%.
Phosphorus (P) and Sulfur (S)
These elements are considered impurities in steel:
-
Phosphorus can increase strength but reduces ductility and toughness, increasing brittleness.
-
Sulfur tends to form weak spots, making the steel prone to cracking.
Both elements should be minimized:
-
Typical phosphorus composition: less than 0.05%.
-
Typical sulfur composition: less than 0.05%.
Types of Rebar and Their Chemical Composition
Different grades and types of rebar are designed for specific applications and environmental conditions:
-
Carbon Steel Rebar: Most common type, standard chemical composition.
-
Epoxy-Coated Rebar: Similar chemical makeup to standard steel but coated to prevent corrosion.
-
Stainless Steel Rebar: Contains high chromium (Cr), nickel (Ni), and molybdenum (Mo) for maximum corrosion resistance, used especially in marine and harsh environments.
Typical Chemical Composition of Common Grades
-
ASTM A615 (Standard Carbon Steel):
-
Carbon: max 0.30%
-
Manganese: 0.60–1.00%
-
Silicon: around 0.15–0.30%
-
-
ASTM A706 (Low Alloy Steel):
-
Carbon: max 0.30%
-
Manganese: around 1.50%
-
Contains low levels of phosphorus and sulfur.
-
-
ASTM A955 (Stainless Steel Rebar):
-
Chromium: 10.5–12%
-
Nickel: 3–5%
-
Molybdenum: 1–2.5%
-
How the Chemical Composition Affects Rebar Performance
Strength and Ductility
A balanced carbon-manganese composition is crucial:
-
Higher strength requires controlled carbon levels.
-
Ductility and flexibility require lower carbon and balanced manganese and silicon contents.
Corrosion Resistance
Corrosion is a significant factor influencing the longevity of concrete structures:
-
Higher chromium and nickel content (stainless steel) provides superior corrosion resistance.
-
Proper epoxy coatings or corrosion inhibitors can compensate for standard carbon steel’s susceptibility to corrosion.
Weldability and Workability
-
Lower carbon and phosphorus contents enhance weldability and ease shaping processes.
-
Excessive sulfur and phosphorus content reduces weldability, making construction more complicated and costly.
Industry Standards and Regulations
Following international standards ensures quality, safety, and consistency:
-
ASTM Standards (e.g., ASTM A615, A706, A955): Define acceptable chemical compositions, tensile strengths, and ductility levels.
-
ISO Standards (e.g., ISO 6935): Specify manufacturing processes and acceptable chemical ranges.
Ensuring compliance with these standards protects structures from premature failures and reduces legal and financial liabilities.
Practical Tips for Selecting Rebar Based on Chemical Composition
-
Evaluate Environmental Conditions: Marine or humid environments demand stainless steel or coated rebar.
-
Check Project Requirements: Structural engineers must specify precise chemical composition criteria based on structural demands.
-
Request Mill Certificates: Verify chemical analysis reports to ensure compliance with standards.
Expert Advice: Consulting with metallurgical or structural engineering experts can significantly improve your selection, enhancing structural safety and reducing long-term maintenance costs.
Conclusion
The chemical composition of rebar profoundly influences construction quality, durability, and safety. By understanding how different elements affect steel performance, builders and engineers can make informed choices to optimize their projects. Always prioritize quality, compliance with international standards, and match rebar types to the specific needs of your project environment.
Take Action: Did you find this guide helpful? Share your experience or ask questions in the comments section below. Don’t forget to subscribe for more practical tips and insights on construction materials and techniques!