- April 23, 2025
- Posted by: wellcoindustries
- Category: Rebar
Introduction
Concrete lasts as long as its steel skeleton stays intact—but rust never sleeps. Corrosion costs the U.S. over $22 billion annually in bridge repairs alone, driving engineers to seek reinforcement that will not oxidize. Composite rebar technologies, made from fiber-reinforced polymers (FRP), promise a non-corrosive, lightweight alternative that is transforming how builders design and maintain concrete structures. This guide walks you through the latest composite rebar options, their benefits, and how to deploy them confidently on site.
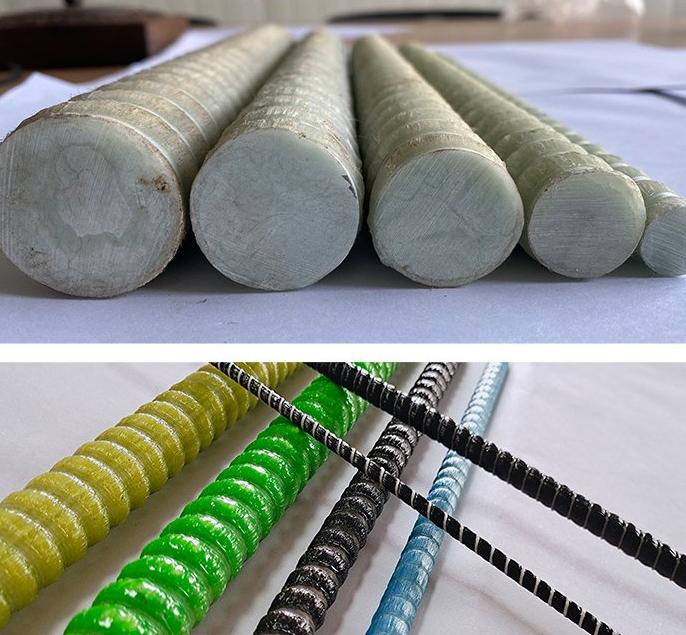
Understanding Composite Rebar Technologies
Composite—or FRP—rebar consists of continuous strands of high-strength fibers embedded in a thermoset resin matrix and formed through pultrusion or filament winding. Because the fibers carry almost the entire tensile load, designers can tailor strength, stiffness, and durability by choosing among four primary fiber families:
-
Glass (GFRP) – economical, widely available
-
Basalt (BFRP) – naturally fire-resistant, similar cost to GFRP
-
Carbon (CFRP) – highest stiffness-to-weight ratio, premium price
-
Aramid (AFRP) – exceptional impact and fatigue resistance
Hybrid lay-ups combine two or more fiber types to balance cost and performance, while nano-enhanced epoxy resins increase bond strength with concrete. Standards such as ACI 440.6-08 specify minimum properties and testing methods for carbon and glass FRP bars, giving specifiers a clear compliance path.
Advantages over Traditional Steel Reinforcement
Corrosion Resistance
Steel begins corroding the moment chloride ions or carbonation reach the bar. FRP’s non-metallic nature eliminates this mechanism, extending the service life of reinforced concrete well beyond the 75-year design horizon many agencies now require.
Weight Reduction & Handling
FRP bars weigh roughly one-quarter that of equivalent steel.Crews can carry more material, reduce crane picks, and cut transportation costs—especially valuable for remote or elevated sites.
High Tensile Strength & Electromagnetic Neutrality
GFRP bars deliver tensile strengths of 600–1 000 MPa, easily surpassing Grade 60 steel, while CFRP can reach 2 000 MPa. Because they are non-conductive and non-magnetic, composite rebars are ideal for MRI facilities, aluminum smelters, and high-voltage environments.
Cutting-Edge Composite Rebar Technologies in 2025
Basalt-Fiber-Reinforced Polymer (BFRP)
BFRP uses volcanic rock fibers that resist alkali attack and UV exposure better than E-glass. Manufacturers have aligned their products to ACI 440 design equations, and several DOTs now allow BFRP in bridge decks.
Carbon-Fiber-Reinforced Polymer (CFRP)
Once reserved for aerospace, CFRP prices have fallen 18 % since 2020, making it viable for high-fatigue applications like stay-in-place bridge panels.
Glass-Fiber-Reinforced Polymer (GFRP)
GFRP remains the workhorse of the market and is projected to hit US $416 million by 2030, up from US $226 million in 2024—an annual growth rate of 10.7 %.
Hybrid & Nano-Enhanced Composites
Producers are blending carbon and basalt fibers with graphene-infused resins to raise shear capacity by 25 % without sacrificing cost competitiveness, opening doors to taller precast façade panels and thinner bridge deck overlays.
Practical Applications and Case Studies
-
Transportation Infrastructure: Florida DOT built the 2023 Gandy Boulevard overpass with GFRP top-mat reinforcement; modeling predicts a 100-year service life with zero corrosion repairs.
-
Marine & Waterfront: The Port of Rotterdam uses BFRP dowels in its quay walls to withstand saltwater immersion and freeze–thaw cycles.
-
Precast Products: Canadian precasters now embed CFRP cages in insulated wall panels, trimming panel thickness by 15 % while maintaining composite action.
Field performance confirms that composite rebar technologies sharply reduce maintenance closures and extend structural life cycles.
Cost Considerations and ROI
The initial price of GFRP ranges from US $2.20–2.80 per kg, about 1.6 × steel, but owners recoup the premium through lower labor, shipping, and maintenance outlays. Global market analysts forecast a CAGR of 11.97 % between 2024 and 2032 as economies of scale take hold.A life-cycle cost model for coastal bridge decks showed 35 % savings over 75 years when FRP replaced epoxy-coated steel, even with conservative discount rates.
Installation Tips and Best Practices
-
Storage & Handling: Keep bars elevated and covered to protect from UV and mechanical damage.
-
Cutting: Use a diamond-grit blade or carbide burr—heat is the enemy of the resin matrix.
-
Bending: Order factory-formed shapes; field bending is not recommended except with thermoplastic FRP variants.
-
Couplers & Anchors: Threaded GFRP couplers or headed studs develop full strength without compromising corrosion immunity.
-
Quality Control: Reference ACI 440.5 and ICC-ES AC454 for inspection criteria; verify bar diameter, fiber volume fraction, and surface finish before placement.
Conclusion & Next Steps
Composite rebar technologies give builders a powerful tool to combat corrosion, accelerate schedules, and reduce life-cycle costs. By understanding the strengths of GFRP, BFRP, CFRP, and emerging hybrids—plus applying the handling and installation tips above—project teams can confidently specify FRP reinforcement in everything from parking garages to pier caps.
Ready to future-proof your next concrete project? Share your thoughts or questions in the comments, and subscribe to our newsletter for more actionable insights on advanced construction materials.