- December 4, 2024
- Posted by: wellcoindustries
- Category: Rebar
Introduction
Reinforced concrete is a cornerstone of modern construction, and at its heart lies rebar, the material responsible for strengthening and stabilizing structures. Traditional steel rebar has been the standard for decades, but with advancements in materials science, a new contender has emerged: FRP construction rebar. FRP, or Fiber-Reinforced Polymer, offers a revolutionary alternative to steel with superior properties, particularly in challenging environments. This guide will introduce you to FRP rebar, explaining its composition, benefits, and the transformative impact it is having on the construction industry.
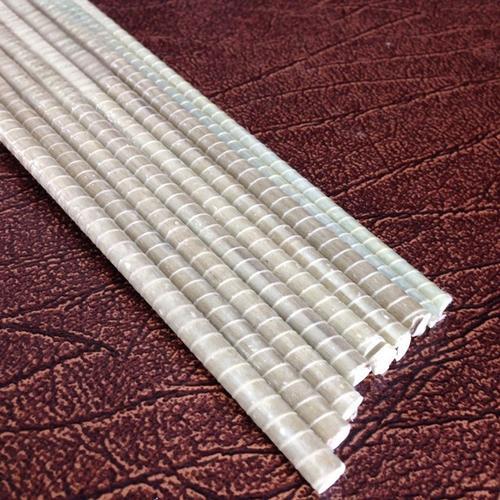
Understanding FRP Rebar
Definition and Composition of FRP Rebar
FRP rebar is a composite material made from high-strength fibers (such as glass, carbon, or aramid) embedded in a polymer matrix. This combination creates a lightweight yet incredibly durable material that resists corrosion, making it ideal for reinforcing concrete.
Types of Fibers Used
- Glass Fibers (GFRP): Most common and cost-effective, offering excellent strength and durability.
- Carbon Fibers (CFRP): Known for superior stiffness and strength, though more expensive.
- Aramid Fibers (AFRP): Lightweight and heat-resistant, used in specialized applications.
Key Differences Between FRP and Traditional Steel Rebar
- Steel rebar corrodes over time, especially in marine or chemical environments, while FRP is inherently corrosion-resistant.
- FRP is non-conductive and non-magnetic, making it suitable for applications requiring electromagnetic neutrality.
- FRP’s weight is a fraction of steel, facilitating easier transportation and installation.
Advantages of FRP Rebar
Corrosion Resistance
One of the most significant advantages of FRP rebar is its immunity to rust, which extends the lifespan of structures in harsh environments, such as coastal regions or chemical plants.
Lightweight and High Strength
FRP is about one-fourth the weight of steel but can match or exceed its tensile strength, making it easier to handle on-site without compromising performance.
Long-Term Cost-Effectiveness
While the initial cost of FRP rebar may be higher, its durability and low maintenance requirements result in significant savings over a structure’s lifespan.
Non-Conductive and Non-Magnetic
FRP is ideal for projects requiring insulation from electrical and magnetic interference, such as MRI rooms and high-voltage substations.
Manufacturing Process
How FRP Rebar is Made
The production process involves pulling fibers through a resin bath and then curing them into the desired shape under controlled heat and pressure. This technique, known as pultrusion, ensures uniform quality and strength.
Key Quality Standards for FRP Production
FRP rebar must meet strict standards, such as ASTM D7205 and ISO 10406, to ensure its mechanical and physical properties align with safety and performance requirements.
Applications of FRP Rebar
Use in Bridges and Highways
FRP rebar is widely used in bridges, where its corrosion resistance prevents deterioration caused by de-icing salts and humidity.
Marine Structures and Waterfronts
In environments exposed to saltwater, such as docks and seawalls, FRP outperforms steel, providing longevity and structural integrity.
Concrete Reinforcement in Buildings
From parking garages to skyscrapers, FRP rebar strengthens concrete structures while reducing maintenance costs over time.
Use in Corrosive Environments
Chemical plants, wastewater treatment facilities, and industrial zones benefit from FRP’s resistance to aggressive chemical reactions.
Comparison: FRP vs. Steel Rebar
Feature | FRP Rebar | Steel Rebar |
---|---|---|
Corrosion Resistance | Excellent | Poor |
Weight | Lightweight | Heavy |
Magnetic Properties | Non-magnetic | Magnetic |
Initial Cost | Higher | Lower |
Maintenance Costs | Low | High |
Challenges of FRP Rebar
Limitations in Fire Resistance
FRP’s polymer matrix can degrade at high temperatures, requiring additional fireproofing measures in certain applications.
Higher Initial Costs
The upfront investment for FRP rebar is higher than steel, though it is offset by long-term savings.
Structural Compatibility Concerns
Designing with FRP requires adjustments in engineering calculations due to its different modulus of elasticity compared to steel.
Innovations in FRP Rebar
New Technologies Improving FRP Performance
Recent advancements include hybrid rebar, which combines FRP with other materials to enhance performance and address limitations like fire resistance.
Hybrid Rebar
The development of hybrid systems incorporating FRP and steel has opened new possibilities for cost-effective and versatile reinforcement solutions.
How to Choose FRP Rebar
Factors to Consider
- Project requirements, including environmental conditions and load-bearing needs.
- Budget constraints and long-term cost considerations.
Key Suppliers and Certifications
Look for manufacturers certified under industry standards like ASTM and ISO to ensure quality.
Environmental Impact
Sustainability of FRP Materials
FRP production has a lower carbon footprint compared to steel, contributing to greener construction practices.
Reducing Carbon Footprints
Using FRP rebar minimizes the need for frequent repairs and replacements, further lowering environmental impact.
FRP Rebar Installation
Guidelines for Handling and Installation
FRP’s lightweight nature simplifies installation, but care must be taken to avoid damaging the fibers during handling.
Best Practices
Use proper tying and spacing techniques to ensure FRP rebar stays secure within the concrete.
Case Studies
Successful Projects Utilizing FRP Rebar
- The Chiquita Bridge in Honduras stands as a testament to the durability of FRP in a humid, salty environment.
- Parking garages in Canada have used FRP to withstand freezing temperatures and de-icing salts.
Lessons Learned
These projects demonstrate the importance of proper installation techniques and the long-term benefits of FRP rebar.
FAQs
- What is FRP construction rebar used for?
It is used for reinforcing concrete in environments prone to corrosion and requiring durability. - How long does FRP rebar last?
Properly installed FRP rebar can last over 100 years, depending on environmental conditions. - Is FRP rebar better than steel?
Yes, particularly in corrosive environments, but steel may still be preferred in fire-prone areas. - Can FRP rebar be used in residential buildings?
Absolutely, especially in foundations and areas exposed to moisture. - How does FRP rebar handle extreme temperatures?
FRP performs well in cold environments but requires fireproofing in high-temperature applications. - What are the limitations of FRP rebar?
Its higher cost and lower fire resistance are notable drawbacks.
Conclusion
FRP construction rebar represents a cutting-edge solution for modern infrastructure needs. Its unique properties, such as corrosion resistance, lightweight nature, and durability, make it a strong contender to replace traditional steel rebar in many applications. As the construction industry evolves, adopting FRP rebar will not only enhance structural performance but also promote sustainability.
Ready to revolutionize your next project? Explore FRP construction rebar today!