- October 30, 2024
- Posted by: wellcoindustries
- Category: Rebar
Introduction
In construction, the materials used must balance strength, durability, and efficiency to withstand the test of time. Rebar, or reinforcing bar, is one of the essential elements, used to provide structural support and increase the tensile strength of concrete. Traditionally, steel rebar has dominated the industry; however, new materials, like fiberglass rebar, are transforming how builders approach construction. One of the defining characteristics of fiberglass rebar is its weight, which is significantly lighter than steel. This article explores fiberglass rebar weight, explaining why it’s a game-changer in modern construction by offering lighter, stronger, and corrosion-resistant alternatives to traditional rebar options.
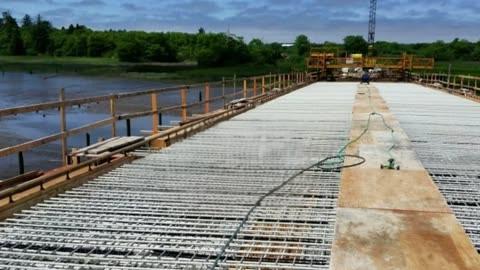
What is Fiberglass Rebar?
Fiberglass rebar, also known as Glass Fiber Reinforced Polymer (GFRP) rebar, is a composite material designed to replace conventional steel rebar in many applications. Produced by combining high-strength glass fibers with a polymer resin, this rebar is molded into rods that resemble steel rebar in shape but differ in properties. One of its most distinct characteristics is its lightweight nature, which sets it apart from heavier steel rebar.
Where steel rebar is dense and prone to corrosion, fiberglass rebar offers a rust-resistant, lightweight alternative, helping extend the lifespan of structures, especially in environments exposed to moisture or chemicals. Its unique weight properties not only make it easier to transport but also reduce the labor required during installation, leading to increased efficiency and cost savings in construction projects.
Why Fiberglass Rebar Weight Matters
The lighter weight of fiberglass rebar has significant implications for construction efficiency and logistics. Traditional steel rebar is often cumbersome to handle, transport, and install due to its weight, which can add to labor costs and require heavier machinery on-site. By contrast, fiberglass rebar is around one-fourth the weight of steel, allowing for faster, more efficient transport and handling.
Here’s how fiberglass rebar weight impacts construction:
- Reduced Shipping Costs: Because fiberglass rebar is lighter, it lowers transportation costs, especially for large-scale projects requiring high volumes of rebar.
- Ease of Installation: Contractors benefit from easier handling on-site, as fiberglass rebar can often be managed without heavy equipment. This not only speeds up construction times but also reduces labor intensity.
- Safety Benefits: The reduced weight minimizes the strain on workers, potentially lowering the risk of lifting-related injuries and making it safer for teams to work with, particularly on elevated or confined sites.
These advantages make fiberglass rebar an attractive option for projects where minimizing weight without compromising strength is essential.
Comparing Fiberglass Rebar Weight to Steel Rebar
When comparing fiberglass rebar weight to steel rebar, the differences are stark. On average, fiberglass rebar weighs only 25% of what an equivalent steel bar would weigh. For example, a 10-foot length of steel rebar might weigh around 10 pounds, while the same length of fiberglass rebar would weigh only 2.5 pounds. This weight reduction translates to tangible savings in various aspects of construction.
But weight isn’t the only factor to consider. Here’s how fiberglass rebar stacks up in terms of strength-to-weight ratio:
- Strength-to-Weight Superiority: Fiberglass rebar has an excellent strength-to-weight ratio, meaning it offers impressive tensile strength despite being lighter. This allows it to perform as well as, if not better than, steel in many applications.
- Resistance to Environmental Degradation: Steel rebar is prone to rust and corrosion, which can weaken its structural integrity over time. Fiberglass rebar, however, is corrosion-resistant, ensuring that it maintains its strength longer, especially in humid, marine, or chemically aggressive environments.
Due to its weight and durability, fiberglass rebar is especially favored in applications that demand high performance under challenging conditions, such as coastal construction and marine installations.
Additional Benefits of Fiberglass Rebar Beyond Weight
While weight is a significant advantage, fiberglass rebar offers several other benefits that make it suitable for diverse construction projects:
- Corrosion Resistance: One of the most notable properties of fiberglass rebar is its resistance to corrosion. Unlike steel, which rusts over time when exposed to moisture, fiberglass rebar is inherently resistant to water and chemical corrosion. This makes it ideal for marine and underground applications.
- High Tensile Strength: Fiberglass rebar is not only lighter but also maintains high tensile strength, providing robust support in structural applications. This combination of lightweight and strength makes it versatile across various settings, from road barriers to building foundations.
- Thermal and Electrical Insulation: Fiberglass rebar is non-conductive, making it suitable for projects that require electrical insulation, such as utility installations and high-voltage power stations.
These benefits, coupled with its reduced weight, make fiberglass rebar a compelling choice for projects seeking sustainable, long-lasting solutions.
Applications of Lightweight Fiberglass Rebar
Fiberglass rebar’s unique properties lend themselves to several construction applications where weight, durability, and resistance to environmental factors are critical. Some ideal uses include:
- Marine Construction: In projects near or in water, fiberglass rebar’s resistance to saltwater corrosion makes it a superior choice.
- Highway Infrastructure: Lightweight fiberglass rebar is frequently used in road and bridge construction, particularly in corrosive or chemically aggressive soils.
- Foundation Work: For buildings and infrastructure requiring a long lifespan with minimal maintenance, fiberglass rebar offers durability and lightweight advantages that ease the installation process.
- Power and Utility Projects: Since fiberglass is non-conductive, it is widely used in electrical and utility projects that demand insulation.
Each of these applications highlights how fiberglass rebar weight contributes to practical construction solutions that prioritize both durability and efficiency.
Conclusion
In the evolving landscape of construction materials, fiberglass rebar stands out for its combination of lightweight, strength, and resistance to corrosion. By choosing fiberglass over traditional steel rebar, project managers and contractors can achieve reduced costs, improved safety, and greater longevity in structures. These advantages make it an increasingly popular choice in sectors ranging from marine construction to highway infrastructure.
As demand for efficient, sustainable materials grows, considering fiberglass rebar for your next project could help streamline construction processes, minimize costs, and extend the lifespan of structures. Embrace the benefits of fiberglass rebar weight to optimize both efficiency and durability in modern construction.