- February 26, 2025
- Posted by: wellcoindustries
- Category: Rebar
1. Introduction
Concrete structures around the world rely on reinforcement bars to ensure strength and long-term durability. Traditionally, steel has dominated this market. However, glass FRP rebar is emerging as a modern alternative with the promise of better corrosion resistance, reduced maintenance, and increased lifespan. In this article, we compare glass FRP rebar and steel to help you decide which option makes the most sense for your construction needs.
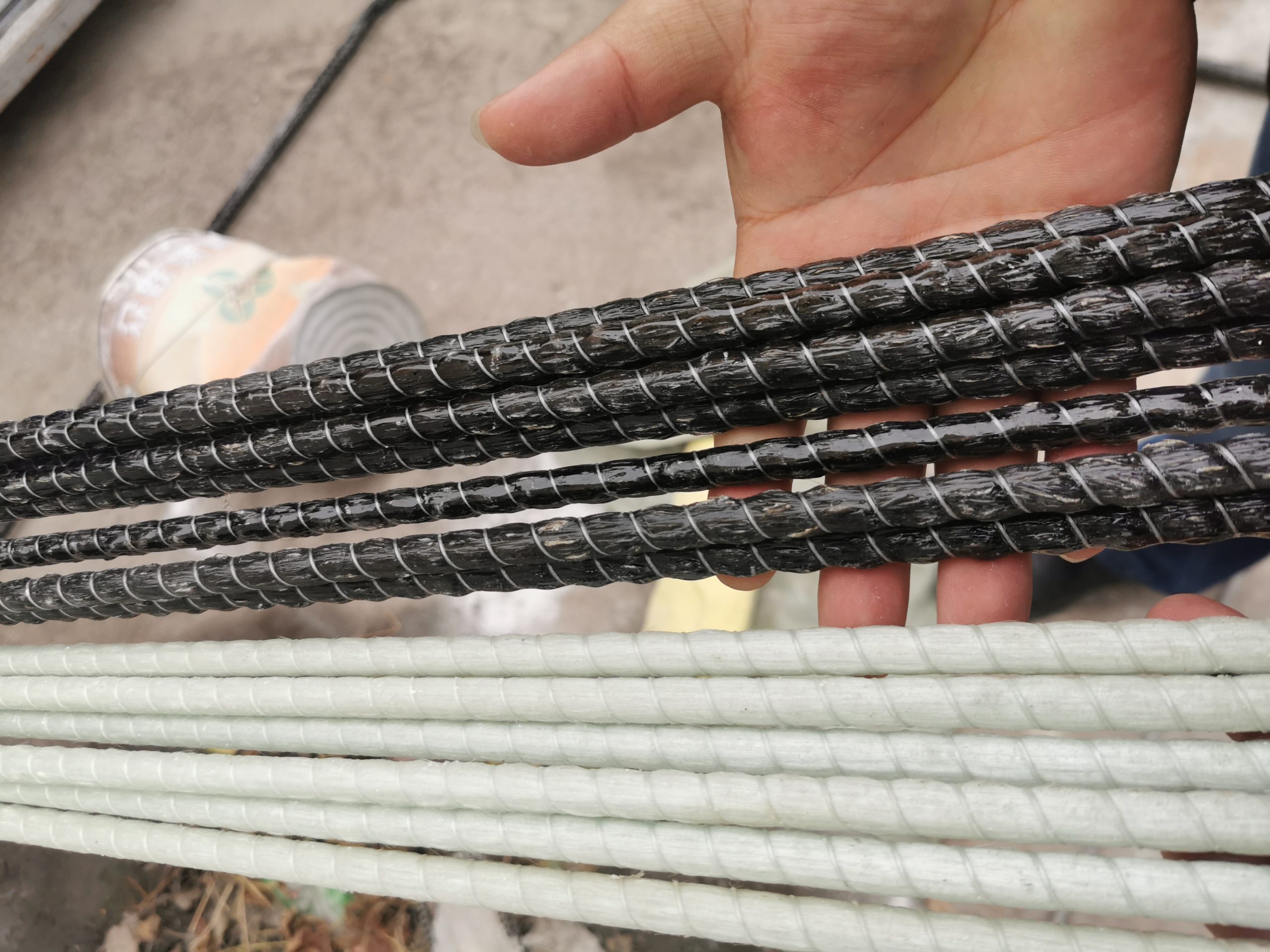
2. The Basics of Reinforcement Bars
2.1 Traditional Steel Rebar
For decades, steel rebar has been the go-to choice for reinforcing concrete. It has a high tensile strength that compensates for concrete’s inherent weakness in tension. Steel is also relatively easy to produce and source, which helps keep costs down in many parts of the world.
- History of steel rebar use: Steel has a proven track record going back over a century, giving engineers confidence in its performance.
- Common challenges: Despite its popularity, steel rebar is susceptible to corrosion, especially in environments with high moisture or exposure to de-icing salts. Over time, rust can weaken the structural integrity of a building or bridge.
2.2 Emergence of Glass FRP Rebar
Glass Fiber Reinforced Polymer (GFRP), commonly referred to as glass FRP, is composed of glass fibers embedded in a polymer resin matrix. This results in a lightweight, non-corrosive reinforcement solution that can significantly prolong the lifespan of concrete structures.
- What makes it different: Glass FRP rebar is approximately one-quarter the weight of steel, making transportation and handling much easier.
- Growing adoption: According to a report by the National Composites Center, the use of composite materials in construction is projected to increase by 8% annually due to growing awareness about corrosion-related costs.
3. Durability & Corrosion Resistance
One of the most compelling reasons to choose glass FRP rebar over steel is its natural resistance to corrosion. When steel rusts, it expands and creates cracks in the concrete around it. Over time, those cracks can compromise an entire structure.
- Corrosion vulnerability: Steel is prone to rust, especially in coastal areas or places where road salt is used. Concrete’s pH can also change over decades, increasing the likelihood of steel corrosion.
- Glass FRP’s advantage: Glass FRP rebar, on the other hand, is impervious to moisture and chemicals. This means it won’t rust or degrade in harsh conditions, significantly reducing maintenance and repair costs.
4. Cost Considerations
Cost is often the first factor that comes to mind when planning a construction project. While steel rebar is typically cheaper at the initial purchase, there are other factors to consider:
- Upfront costs: Steel rebar usually costs less at the time of purchase. Glass FRP rebar may have a slightly higher price tag due to the manufacturing process of composite materials.
- Long-term savings: Because glass FRP rebar does not corrode, it can save money over the life of a project. Reduced need for repairs, especially in corrosive environments, often offsets the initial higher cost.
- Maintenance and downtime: In large-scale infrastructure projects—such as bridges or tunnels—maintenance can be expensive and disruptive. Using corrosion-resistant rebar from the start can minimize these interruptions and their associated costs.
5. Strength & Performance
Both steel and glass FRP rebar serve the same fundamental purpose of reinforcing concrete, but their strength characteristics differ:
- Tensile strength: Glass FRP rebar has a high tensile strength, often comparable to or greater than steel. This quality ensures that it effectively resists tension forces in concrete.
- Weight-to-strength ratio: Glass FRP rebar boasts an impressive weight-to-strength ratio. It’s notably lighter than steel, which can be beneficial when working with high-rise buildings or large-scale transportation of materials.
- Elastic modulus: Steel has a higher elastic modulus than glass FRP, meaning it deforms less under stress. This can be advantageous in certain types of structures where stiffness is crucial. However, engineers can design around the different modulus properties of glass FRP rebar by adjusting structural dimensions.
6. Installation & Handling
Another aspect to consider when selecting rebar is how easily it can be transported, cut, and installed:
- Steel rebar: Workers are generally well-versed in using steel rebar, and specialized tools to cut and bend steel are widely available. However, steel’s weight can increase shipping costs and make on-site handling more labor-intensive.
- Glass FRP rebar: Glass FRP rods are much lighter, simplifying transportation and reducing the risk of injuries related to heavy lifting. They can also be cut using common power tools equipped with diamond blades. Bending is often done at the manufacturing stage, as field bending can be limited depending on the product specifications.
7. Sustainability and Environmental Impact
In recent years, the construction industry has been under pressure to adopt greener, more sustainable practices:
- Steel production: While steel is recyclable, its manufacturing process is energy-intensive and can result in high carbon emissions.
- Glass FRP production: The production of glass FRP rebar consumes less energy and emits fewer greenhouse gases compared to steel. Additionally, the longer lifespan and reduced maintenance needs of glass FRP rebar contribute to lower environmental impact over time.
- Longevity factor: Because glass FRP rebar doesn’t corrode, structures built with it can have an extended service life, reducing the need for early repairs or replacements.
8. Practical Applications
Glass FRP rebar is particularly beneficial in:
- Marine environments: Ports, docks, and waterfront structures face constant exposure to saltwater, making them prime candidates for corrosion-resistant rebar.
- Bridges and highways: De-icing salts and harsh weather conditions accelerate steel corrosion, leading to costly repairs. Glass FRP rebar can mitigate these issues.
- Water treatment plants: Facilities with high chemical exposure can benefit from using rebar that is resistant to deterioration.
- Architectural features: When designing complex structures or unique architectural elements, lightweight and easily moldable materials can significantly simplify the process.
9. Conclusion
When deciding between glass FRP rebar and steel, the choice hinges on factors like environment, long-term maintenance, and budget constraints. Steel rebar may be less expensive initially and has a longstanding history in construction. However, glass FRP rebar’s superior corrosion resistance, reduced weight, and comparable tensile strength can result in substantial savings over the lifecycle of a project—especially in corrosive or high-maintenance environments.
If you’re looking to minimize future repair costs, reduce environmental impact, and improve the longevity of your concrete structures, glass FRP rebar might be the better choice. Before making a final decision, consider consulting with structural engineers and suppliers to discuss the specific requirements of your project.
Ready to take the next step? Leave a comment below with any questions you might have about glass FRP rebar, or share this article with colleagues who are also exploring new ways to reinforce their concrete projects.