- February 19, 2025
- Posted by: wellcoindustries
- Category: Rebar
1. Introduction
In modern construction, FRP rebar tensile strength has become a focal point for engineers and builders seeking stronger and more durable alternatives to traditional steel rebar. By comparing FRP (Fiber Reinforced Polymer) directly to steel, industry professionals can determine the most efficient way to enhance structural integrity while also addressing long-term durability needs. This article dives into the key differences between FRP and steel rebar tensile strength, examining factors such as material composition, environmental impact, and practical applications.
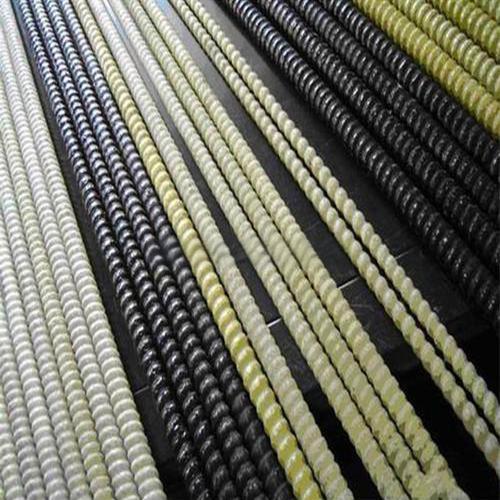
2. Understanding Rebar Strength
Before exploring how FRP rebar compares to steel, it’s important to understand what rebar strength entails. In simple terms, tensile strength refers to the amount of stress a material can withstand before breaking. When used in concrete, rebar provides the critical reinforcement needed to offset concrete’s inherent weakness in tension.
2.1 FRP Rebar Tensile Strength
- Composition: FRP rebars are typically made from a combination of carbon, glass, or basalt fibers bound by a polymer resin (such as epoxy or vinyl ester). These fibers contribute significantly to the bar’s tensile strength.
- High Strength-to-Weight Ratio: One of the standout characteristics of FRP rebar is its impressive strength-to-weight ratio. According to the American Concrete Institute (ACI), certain types of glass-fiber-reinforced polymer (GFRP) can achieve tensile strengths that surpass 100,000 psi while remaining much lighter than steel.
- Non-Corrosive Nature: FRP rebars do not rust or corrode, maintaining their tensile capacity over an extended period. This feature is particularly beneficial in structures exposed to moisture, chlorides, or other corrosive agents.
2.2 Steel Rebar Tensile Strength
- Traditional Material: Steel is the more commonly used and time-tested reinforcement material in construction. Its tensile strength typically ranges from 60,000 to 80,000 psi for mild steel rebar, although higher grades can reach well above 100,000 psi.
- Ductility Advantage: Steel’s ductility allows it to yield before fracturing, providing a warning period during which structural failure can be mitigated or prevented.
- Susceptibility to Corrosion: Unlike FRP, steel can corrode over time when exposed to water, salt, or chemicals. Rust expansion can cause cracking and spalling in concrete, leading to potential structural issues if not properly addressed.
3. Key Factors Influencing Tensile Strength
To fully appreciate how FRP rebar tensile strength compares to steel, it’s vital to consider the underlying factors that determine a reinforcement material’s performance.
3.1 Material Composition
- Fiber Type (FRP): The type of fiber in FRP bars—glass, carbon, or basalt—affects tensile strength. Carbon fibers generally offer the highest tensile strength, while glass fibers provide a cost-effective balance of strength and affordability.
- Steel Grade: Steel rebars vary in grade (e.g., ASTM A615 Grade 60, Grade 75), which impacts their yield strength and ultimate tensile strength. Engineers often select a grade based on project requirements and budget constraints.
- Resins and Coatings: In FRP rebar, the resin binding the fibers plays a crucial role in maintaining structural integrity. Similarly, steel rebar can be coated with epoxy or galvanized to reduce corrosion.
3.2 Environmental Considerations
- Exposure to Chemicals: In highly acidic or alkaline environments, steel rebar may degrade faster without protective measures. FRP remains largely inert, maintaining tensile capacity for longer.
- Moisture and Salt: Coastal or marine structures face high humidity and salt exposure, making corrosion-resistant materials like FRP particularly valuable.
- Temperature Fluctuations: Both FRP and steel rebar can be affected by extreme temperatures. However, steel tends to expand or contract more predictably, whereas certain FRP compositions can be more sensitive to heat.
4. Comparing FRP Rebar vs. Steel Rebar
4.1 Performance Under Stress
- Tensile Strength: In laboratory tests, FRP rebar has demonstrated tensile strengths that can exceed many grades of steel, especially when premium fibers are used. For example, carbon-fiber-reinforced bars can achieve tensile strengths upwards of 150,000 psi.
- Yielding and Brittle Failure: Steel rebar’s ductility allows it to deform (yield) before breaking, providing a safety buffer. FRP rebar, on the other hand, does not yield in a traditional sense and can fail suddenly if overloaded. Engineers account for this by using higher safety factors or combined reinforcement strategies.
- Elastic Modulus: Steel typically has a higher modulus of elasticity, meaning it resists deformation better under the same load. FRP rebars tend to be more flexible, so designers must adjust structural plans to accommodate for increased deflection.
4.2 Longevity and Corrosion Resistance
- Maintenance and Lifecycle: The non-corrosive nature of FRP significantly reduces the need for maintenance in harsh environments. Structures reinforced with FRP can remain serviceable much longer compared to those with steel that is left unprotected.
- Cost Over Time: Initially, FRP may have a higher upfront cost due to the materials and manufacturing processes. However, considering the reduced maintenance and longer service life, the overall lifetime cost can be more favorable compared to steel.
- Case Study – Bridges: According to a study published by the National Cooperative Highway Research Program (NCHRP), bridges reinforced with FRP rebar exhibit longer service lives and lower repair costs over time, especially when exposed to deicing salts and constant moisture.
5. Practical Applications and Use Cases
Knowing how FRP and steel differ in tensile strength can help determine which projects benefit most from each material.
5.1 FRP in Marine and Coastal Structures
- Saltwater Exposure: FRP’s corrosion-resistant properties make it a top choice for piers, docks, and other marine applications. Its high FRP rebar tensile strength combined with non-corrosive benefits ensures structural integrity against salt-induced damage.
- Reduced Maintenance: Structures in or near the ocean often face significant maintenance costs due to corrosion. FRP rebars can dramatically cut these costs over the lifespan of a project.
5.2 Steel Rebar for Heavy-Duty Projects
- Major Infrastructure: For heavily loaded structures like highways, high-rise buildings, or large-scale industrial complexes, steel rebar’s ductility and well-known track record can offer peace of mind.
- Project Familiarity: Steel is still the industry standard, and many design codes, contractors, and inspectors are more accustomed to working with steel rebar. This can streamline procurement and construction processes.
6. Conclusion
How FRP Rebar Tensile Strength Compares to Traditional Steel largely depends on the project’s specific requirements, environmental conditions, and long-term maintenance goals. FRP rebar often surpasses steel in corrosion resistance and tensile strength (especially with carbon fibers), making it ideal for marine or aggressive environments. Steel rebar, meanwhile, remains the tried-and-true standard for many high-load infrastructure projects, thanks to its ductility and familiarity in the industry.
Ultimately, the choice between FRP and steel rebar requires weighing factors such as cost, structural demands, and lifecycle considerations. By understanding these key distinctions, builders and engineers can make informed decisions to ensure safe, durable, and cost-effective construction.
Call to Action
Have you ever worked on a project where rebar choice made a significant impact? Share your experience in the comments below! If you found this comparison helpful, consider sharing it on social media or subscribing to our newsletter for more in-depth construction insights and updates.