- June 12, 2024
- Posted by: wellcoindustries
- Category: Rebar
FRP (Fiber Reinforced Polymer) rebar is a type of reinforcement material used in concrete structures. It’s known for its high strength, lightweight, and resistance to corrosion, making it a popular choice for construction projects. Understanding the manufacturing process of FRP rebar can help us appreciate its advantages and applications. Here’s a step-by-step look at how FRP rebar is made:
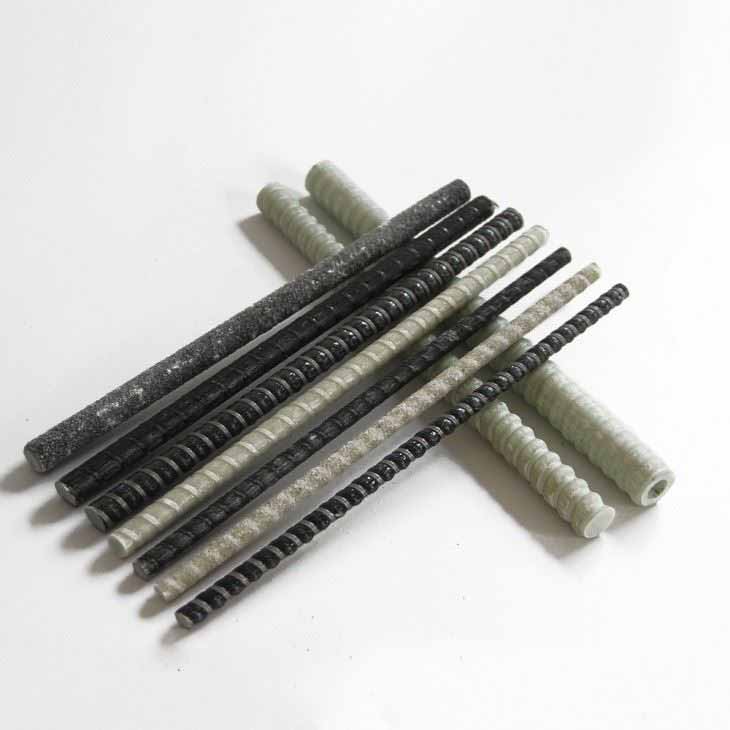
1. Raw Material Preparation
The manufacturing process starts with preparing the raw materials. The main components of FRP rebar are fibers and resin. The fibers, usually made of glass, carbon, or basalt, provide the strength and stiffness, while the resin acts as a binding agent to hold the fibers together. The fibers are often treated with a sizing agent to improve their bonding with the resin.
2. Fiber Winding or Pultrusion
There are two primary methods for creating FRP rebar: fiber winding and pultrusion.
- Fiber Winding: In this method, continuous fibers are wound around a rotating mandrel in a specific pattern. The resin is applied to the fibers during the winding process. This method is typically used for making complex shapes and customized rebar designs.
- Pultrusion: This is the more common method for manufacturing FRP rebar. Continuous fibers are pulled through a resin bath where they are thoroughly impregnated with resin. The impregnated fibers are then pulled through a heated die, which shapes and cures the material into a solid rod. This continuous process allows for the production of long lengths of rebar with consistent quality.
3. Curing
After the fibers are impregnated with resin and shaped, the rebar needs to be cured. Curing involves applying heat to the material to harden the resin. This process can be done in an oven or by passing the rebar through a heated die. Proper curing is essential to ensure the rebar achieves the desired mechanical properties and durability.
4. Surface Treatment
Once the rebar is cured, it undergoes surface treatment. The surface of FRP rebar is often textured or coated with sand to improve its bond with concrete. This step is crucial because the bond between the rebar and the concrete determines the effectiveness of the reinforcement.
5. Cutting and Quality Control
The final step in the manufacturing process is cutting the rebar to the desired lengths. After cutting, each piece of rebar undergoes rigorous quality control tests to ensure it meets industry standards. Tests may include checking the tensile strength, modulus of elasticity, and resistance to environmental factors such as moisture and chemicals.
Conclusion
The manufacturing process of FRP rebar involves several critical steps, from preparing raw materials to quality control. By using advanced techniques like fiber winding and pultrusion, manufacturers can produce high-quality FRP rebar that offers significant advantages over traditional steel rebar, including resistance to corrosion, lightweight, and high tensile strength. Understanding this process helps us appreciate why FRP rebar is becoming an increasingly popular choice in the construction industry.