- December 11, 2024
- Posted by: wellcoindustries
- Category: Rebar
In the world of modern construction, materials are constantly evolving to meet the demands of strength, sustainability, and cost-effectiveness. One such innovation is FRP pultruded rebar, a reinforcement material that is gradually becoming a preferred alternative to traditional steel rebar. Whether you’re an architect, engineer, or contractor, understanding the benefits, applications, and nuances of FRP pultruded rebar is essential for making informed decisions in your building projects. In this ultimate guide, we’ll explore everything you need to know about this game-changing material, from its basic properties and advantages to its growing role in infrastructure and industrial projects.
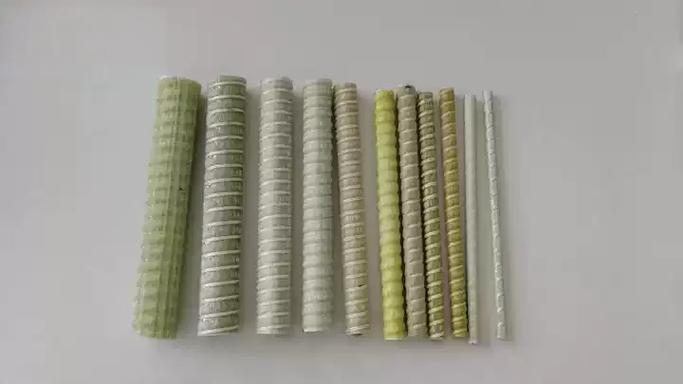
What is FRP Pultruded Rebar?
Definition of FRP Pultruded Rebar
FRP pultruded rebar (Fiber Reinforced Polymer) is a composite material used for reinforcing concrete structures, offering an alternative to traditional steel reinforcement. The material is made from a combination of fiber strands (usually fiberglass) and a polymer resin. Pultrusion is the manufacturing process used to create this material, which involves pulling fiber rovings through a resin bath and curing them in a heated die to form continuous profiles, typically in the shape of rods or bars.
Manufacturing Process of FRP Pultruded Rebar
The production process begins with high-strength fibers, typically fiberglass, which are pulled through a resin bath to saturate the fibers with resin. Once saturated, the composite is pulled through a heated mold where it is cured to form solid rods or bars of rebar. This process ensures that the rebar is both lightweight and incredibly strong. Additionally, it allows for customization in terms of length, diameter, and other specifications.
Benefits of Using FRP Pultruded Rebar in Construction
Durability and Corrosion Resistance
One of the primary advantages of FRP pultruded rebar is its exceptional resistance to corrosion. Unlike traditional steel rebar, which is prone to rusting when exposed to moisture, salts, or other chemicals, FRP rebar remains unaffected by such environmental factors. This makes it particularly valuable for projects in coastal or highly humid areas, where corrosion of steel would lead to costly repairs and shortened lifespans.
Lightweight Nature and Ease of Handling
FRP pultruded rebar is significantly lighter than its steel counterparts, which simplifies transportation and handling on construction sites. Its lightweight nature reduces the risk of injuries, lowers transportation costs, and speeds up the installation process.
Cost-Effectiveness Over Time
While FRP pultruded rebar can have a higher initial cost compared to traditional steel, its longevity and durability lead to lower maintenance costs in the long run. The reduced need for repairs and replacements significantly lowers the overall life cycle costs of structures using FRP rebar.
Environmental Benefits
As the construction industry moves toward sustainability, FRP pultruded rebar offers a more eco-friendly option. The material itself is non-corrosive, leading to less waste, and it is often produced using greener manufacturing processes. Additionally, the reduced need for frequent repairs and replacements further reduces the carbon footprint of structures.
Applications of FRP Pultruded Rebar
Infrastructure and Civil Engineering Projects
FRP pultruded rebar is commonly used in infrastructure projects such as highways, tunnels, and bridges. The rebar’s durability and corrosion resistance are invaluable in environments that are exposed to the elements, chemicals, and heavy traffic loads.
Marine and Coastal Engineering
Marine structures like piers, docks, and seawalls are highly susceptible to the damaging effects of saltwater. FRP pultruded rebar is an ideal solution for these applications, providing long-lasting reinforcement without the risk of rust or corrosion.
Bridges and Highways
The use of FRP pultruded rebar in bridges and highways ensures greater safety and longevity. This rebar can withstand the corrosive effects of de-icing salts used in colder climates, making it perfect for use in roadways and bridges exposed to harsh winter conditions.
Industrial Construction
In industrial construction, FRP rebar is used in the reinforcement of floors, ceilings, and walls, especially in chemical processing plants, water treatment facilities, and factories where environmental factors can rapidly degrade traditional steel.
FRP Pultruded Rebar vs. Steel Rebar: A Comparison
When comparing FRP pultruded rebar to traditional steel, several key differences stand out. While steel rebar is strong and reliable, FRP pultruded rebar offers superior resistance to corrosion, making it more suitable for environments where steel would degrade quickly. FRP rebar also has a lower weight, making it easier to handle and reducing labor costs. In terms of load-bearing capacity, FRP can match or exceed steel in certain applications, though it might be more expensive upfront. However, the long-term benefits, including less maintenance and a longer lifespan, make FRP a highly cost-effective choice in many cases.
How FRP Pultruded Rebar Improves Construction Projects
Enhancing Safety Standards
FRP’s non-conductive and lightweight properties contribute to safer construction sites. These features protect workers and reduce the risks associated with manual handling or electrical hazards.
Speeding Up Construction
The material’s ease of installation shortens construction timelines, lowering labor costs and minimizing project delays.
Supporting Sustainability
Its long lifespan and minimal maintenance requirements make FRP rebar a sustainable choice, reducing the environmental footprint of construction projects.
Challenges in Using FRP Pultruded Rebar
While advantageous, FRP rebar does come with some challenges:
- Technical limitations, such as reduced ductility.
- Supply chain issues, impacting availability in some regions.
- Regulatory hurdles, requiring careful compliance with evolving standards.
Future Trends in FRP Pultruded Rebar
The future is bright for FRP pultruded rebar, with advancements in hybrid materials and increasing adoption in new sectors like renewable energy. As sustainability and durability take center stage, this innovative material is set to become a mainstay in global construction.
FAQs About FRP Pultruded Rebar
Q1: What is the difference between FRP and traditional steel rebar?
FRP rebar is corrosion-resistant, lightweight, and durable, whereas steel rebar is prone to rust and requires frequent maintenance.
Q2: Can FRP pultruded rebar be used in all climates?
Yes, FRP rebar performs well in extreme climates, offering unmatched durability even in harsh conditions.
Q3: How long does FRP pultruded rebar last?
Its lifespan often exceeds that of steel, lasting several decades with minimal maintenance.
Q4: Is FRP pultruded rebar more expensive than steel?
Initially, yes, but its long-term cost savings from reduced maintenance make it more economical.
Q5: Can FRP pultruded rebar be recycled?
Yes, with emerging recycling technologies, FRP materials are becoming increasingly reusable.
Conclusion
The adoption of FRP pultruded rebar is transforming the construction industry, offering enhanced durability, sustainability, and cost-effectiveness. As demand grows, this innovative material will continue to shape the future of building and infrastructure projects.