- July 17, 2024
- Posted by: wellcoindustries
- Category: Other
Introduction
In the ever-evolving construction industry, materials that offer enhanced durability and longevity are highly sought after. One such innovation is FRP (Fiber Reinforced Polymer) rebar. Unlike traditional steel rebar, FRP rebar boasts a range of benefits that make it an attractive choice for various construction projects. This article delves into the world of FRP rebar, exploring its benefits, applications, installation tips, and more.
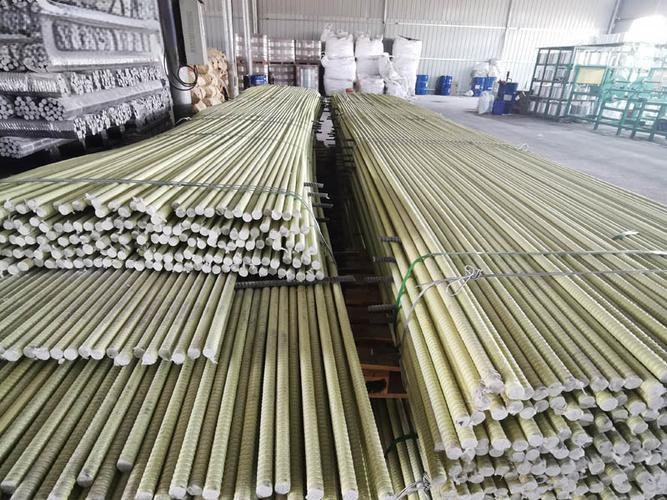
What is FRP Rebar?
FRP rebar is a composite material made from a polymer matrix reinforced with fibers, typically glass, carbon, or basalt. This composition grants it exceptional properties, making it a superior alternative to traditional steel rebar. While steel rebar has been the standard in construction for decades, it is prone to corrosion and deterioration over time, especially in harsh environments. In contrast, FRP rebar is non-corrosive, offering a longer lifespan and reducing maintenance costs.
Benefits of FRP Rebar
- Non-Corrosive Nature: FRP rebar does not rust or corrode, even when exposed to moisture and chemicals, making it ideal for use in environments where steel rebar would typically degrade.
- High Strength-to-Weight Ratio: Despite being lighter than steel, FRP rebar provides comparable, if not superior, tensile strength. This property allows for easier handling and reduced transportation costs.
- Longevity and Durability: The inherent durability of FRP rebar translates to longer-lasting structures, which require less frequent repairs and replacements.
- Cost-Effectiveness Over Time: Although the initial cost of FRP rebar may be higher than steel, the reduction in maintenance and replacement costs over time makes it a more economical choice in the long run.
Applications of FRP Rebar
FRP rebar is versatile and can be used in various construction projects, including:
- Infrastructure Projects: Ideal for highways, bridges, and tunnels where durability is paramount.
- Marine and Waterfront Structures: Its resistance to corrosion makes it perfect for piers, docks, and other marine applications.
- Chemical Plants: FRP rebar’s non-reactive nature makes it suitable for environments exposed to aggressive chemicals.
- Bridges and Tunnels: Used in structural applications where long-term durability is essential.
Installation of FRP Rebar
When installing FRP rebar, it is crucial to follow specific guidelines to ensure optimal performance:
- General Installation Guidelines: Use non-metallic tying materials and avoid sharp bends to maintain integrity.
- Tips for Handling and Cutting: FRP rebar can be cut using diamond blades or carbide-tipped tools. Handle with care to prevent damage to the fibers.
- Safety Considerations: Always wear protective gear when handling FRP rebar to avoid skin irritation from the fibers.
FRP Rebar Manufacturers and Costs
Several manufacturers specialize in producing high-quality FRP rebar, including:
- Unicomposite
- Wellco Industries
The cost of FRP rebar varies depending on factors such as fiber type, diameter, and length. Generally, it is more expensive than steel rebar; however, the long-term savings on maintenance and replacement make it a cost-effective option.
Conclusion
FRP rebar represents a significant advancement in construction materials, offering unmatched durability and longevity. Its non-corrosive nature, high strength-to-weight ratio, and cost-effectiveness make it a compelling choice for various applications. As the construction industry continues to evolve, FRP rebar is poised to play a crucial role in building resilient and long-lasting structures. Consider exploring FRP rebar for your next construction project and experience the benefits firsthand.