- December 18, 2024
- Posted by: wellcoindustries
- Category: Rebar
Introduction
Fiber Reinforced Polymer (FRP) rebar has gained significant popularity in modern construction due to its impressive properties, such as high strength, lightweight nature, and resistance to corrosion. This makes it an ideal reinforcement material for concrete structures exposed to harsh environments, such as bridges, highways, and marine infrastructure. However, despite its advantages, FRP rebar is not immune to failure. One of the most concerning issues is delamination, which occurs when the layers of the FRP rebar begin to separate or peel apart. Delamination can significantly compromise the structural integrity of a concrete structure, leading to potential safety hazards and increased maintenance costs. In this article, we will explore the causes, risks, and solutions associated with FRP rebar delamination.
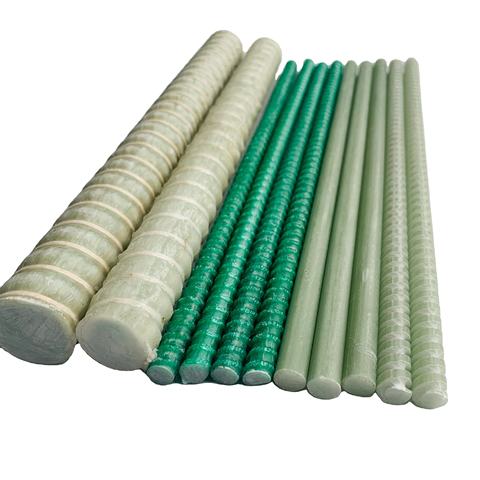
What is FRP Rebar and Why is it Used in Construction?
Key Properties of FRP Rebar
FRP rebar is a composite material made of high-strength fibers (such as glass, carbon, or aramid) embedded in a polymer matrix (usually epoxy or vinyl ester). This combination results in a material that is not only extremely strong and lightweight but also resistant to environmental factors that typically degrade traditional steel rebar, such as corrosion. The high tensile strength of FRP rebar makes it an ideal choice for reinforcing concrete structures that require durability over long periods.
Some of the key properties of FRP rebar include:
- Corrosion resistance: Unlike steel, FRP rebar does not corrode when exposed to water, chemicals, or salt, making it ideal for marine, coastal, and industrial applications.
- Lightweight: FRP rebar is much lighter than traditional steel, reducing the weight of reinforced concrete and making it easier to handle during construction.
- High strength-to-weight ratio: FRP rebar provides a high level of reinforcement without significantly increasing the weight of the structure.
Applications of FRP Rebar in Construction
The unique properties of FRP rebar make it an attractive solution for a wide range of applications, particularly in environments where corrosion and deterioration of steel rebar are major concerns. Common applications of FRP rebar include:
- Bridges: FRP rebar is used in bridge decks, piers, and other structural components to extend the service life of the bridge and reduce maintenance costs.
- Highways and Pavements: FRP rebar can reinforce roadways, reducing the risk of deterioration from harsh weather conditions and chemical exposure.
- Marine Structures: Coastal and marine structures such as docks, piers, and seawalls are ideal for FRP rebar, as they are regularly exposed to saltwater and humidity, which are notorious for causing steel rebar to corrode.
What is Delamination in FRP Rebar?
Defining Delamination
Delamination in FRP rebar refers to the separation of the layers within the composite material, where the fibers and the resin matrix no longer bond effectively. This separation weakens the overall structure of the FRP rebar and can lead to its eventual failure. Delamination typically occurs when the interface between the reinforcing fibers and the polymer matrix begins to degrade, causing the rebar to lose its mechanical properties.
How Delamination Affects the Performance of FRP Rebar
When delamination occurs, it compromises the rebar’s structural performance. The bond between the fibers and resin matrix is essential for transferring stresses within the concrete. If this bond fails, the ability of the rebar to reinforce the concrete diminishes, leading to a reduction in the strength and stability of the entire structure. Delaminated FRP rebar can also experience:
- Reduced Load-Bearing Capacity: The loss of bonding reduces the overall strength of the rebar, leading to a failure in bearing loads that the structure is designed for.
- Increased Risk of Further Damage: Once delamination begins, it can spread through the entire rebar, worsening over time and causing further degradation of the reinforced concrete.
Causes of FRP Rebar Delamination
Manufacturing Defects
One of the primary causes of delamination in FRP rebar is related to manufacturing defects. These defects can include issues such as improper curing, insufficient resin impregnation, or inconsistent fiber alignment during the production process. Any imperfections in the way the composite material is manufactured can result in weak bonding between the fibers and resin, leading to early delamination.
To prevent such issues, manufacturers must adhere to strict quality control measures, including proper curing times, optimal resin application, and consistent fiber placement. Testing and inspection during the manufacturing process are also critical in ensuring that the FRP rebar meets the required standards.
Environmental Factors
Environmental factors, particularly temperature fluctuations and moisture exposure, play a significant role in the delamination of FRP rebar. When FRP rebar is subjected to extreme temperatures, the polymer matrix can expand or contract at different rates than the fibers, putting stress on the bond. Moisture can also weaken the resin and lead to degradation over time. Additionally, chemical exposure (such as from de-icing salts or industrial chemicals) can accelerate the breakdown of the resin, further increasing the risk of delamination.
Mechanical Stress and Load Conditions
FRP rebar is designed to withstand mechanical stresses, but under extreme or fluctuating loads, delamination can still occur. For example, if a structure experiences excessive dynamic loading, such as from heavy traffic on a bridge or vibrations from machinery, the stress on the rebar can exceed the capacity of the material. Rebar subjected to repeated bending or fatigue loading may be more prone to delamination, especially if the rebar has not been properly designed for such conditions.
Risks Associated with Delamination in FRP Rebar
Reduced Structural Integrity
The primary risk associated with delamination in FRP rebar is a reduction in the structural integrity of the concrete structure. Since FRP rebar is intended to reinforce concrete and improve its load-bearing capacity, any loss of strength due to delamination can lead to catastrophic failures, especially in critical infrastructure like bridges and tunnels. The weakened reinforcement can cause cracks, deflections, and even collapse in severe cases.
Increased Maintenance Costs
Delaminated FRP rebar can result in significant maintenance challenges. As the structural integrity of the reinforced concrete decreases, repairs may be required to restore the strength and durability of the structure. In many cases, this can involve costly inspections, repairs, or even full replacements of damaged sections of the concrete, leading to higher long-term maintenance expenses.
Potential Safety Hazards
When delamination occurs in FRP-reinforced structures, it poses potential safety hazards. In particular, infrastructure failures due to weakened rebar can endanger the public. For example, a bridge with delaminated FRP rebar may collapse under heavy traffic, causing significant harm to people and property. Ensuring that FRP rebar maintains its integrity is therefore critical for the safety of construction workers, maintenance personnel, and the general public.
Solutions for Preventing and Addressing FRP Rebar Delamination
Ensuring High-Quality Manufacturing Standards
To minimize the risk of delamination, manufacturers must prioritize quality control throughout the production process. This includes:
- Using high-quality materials and ensuring the correct ratio of resin to fiber.
- Implementing thorough curing processes to ensure proper bonding.
- Conducting regular testing to check for defects like delamination or weak bonding.
Adhering to high manufacturing standards is the first line of defense against delamination and ensures that the FRP rebar can withstand the stresses it is designed to bear.
Proper Installation and Maintenance Practices
Proper installation of FRP rebar is crucial to avoid premature delamination. Ensuring that rebar is placed correctly, with adequate spacing and alignment, can reduce the risk of stress concentrations that could lead to delamination. Additionally, regular inspections and maintenance of concrete structures will help identify early signs of delamination, allowing for timely interventions before serious damage occurs.
Material Enhancements and Innovations
The FRP rebar industry is continuously evolving, with new technologies and materials being developed to reduce the risk of delamination. Some promising innovations include:
- Hybrid Materials: Combining FRP with other materials, such as steel or advanced polymers, to improve bonding and durability.
- Advanced Resin Systems: Developing new resin formulations that are more resistant to environmental degradation and stress.
- Enhanced Bonding Techniques: Improving the chemical bonds between the fibers and resin to prevent separation.
These innovations can help reduce the occurrence of delamination and improve the longevity of FRP-reinforced structures.
Conclusion
FRP rebar offers numerous advantages for reinforced concrete structures, but delamination remains a significant challenge that can compromise its performance. Understanding the causes of delamination, including manufacturing defects, environmental factors, and mechanical stresses, is essential for mitigating its risks. By implementing proper manufacturing practices, ensuring correct installation, and exploring innovative material solutions, the construction industry can reduce the occurrence of delamination and extend the lifespan of structures reinforced with FRP rebar. Maintaining high standards of quality and inspection will ensure that FRP rebar continues to be a reliable and durable choice for modern construction projects.