- June 5, 2024
- Posted by: wellcoindustries
- Category: Rebar
FRP (Fiber Reinforced Polymer) rebar is becoming increasingly popular in construction due to its numerous benefits, including high strength, corrosion resistance, and lightweight properties. In this article, we’ll delve into the FRP rebar production line, highlighting its importance and the steps involved in the manufacturing process.
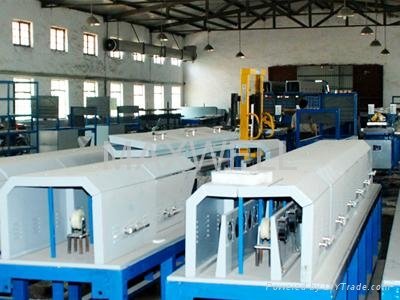
What is FRP Rebar?
FRP rebar is a type of reinforcement bar used in concrete structures. Unlike traditional steel rebar, FRP rebar is made from composite materials, which include a polymer matrix reinforced with fibers such as glass, carbon, or aramid. This composition gives FRP rebar its unique advantages.
Importance of FRP Rebar
The use of FRP rebar in construction projects is growing due to several key benefits:
- Corrosion Resistance: Unlike steel, FRP rebar does not corrode, making it ideal for use in harsh environments, such as coastal areas and chemical plants.
- High Strength-to-Weight Ratio: FRP rebar is much lighter than steel, making it easier to handle and transport, yet it offers high tensile strength.
- Non-Conductive and Non-Magnetic: These properties make FRP rebar suitable for applications where electromagnetic interference needs to be minimized.
Overview of the FRP Rebar Production Line
The production of FRP rebar involves several critical steps to ensure the final product meets industry standards. Here’s an overview of the process:
- Raw Material Preparation
- The production process begins with the preparation of raw materials. High-quality fibers (e.g., glass, carbon) and resin are essential for producing durable FRP rebar.
- Fiber Impregnation
- The prepared fibers are then impregnated with resin. This step ensures that the fibers are thoroughly coated with the resin, which acts as a binding agent.
- Pultrusion Process
- The impregnated fibers are fed into a pultrusion machine. Pultrusion is a continuous process where the fibers are pulled through a heated die. The heat cures the resin, transforming it from a liquid to a solid state, forming the FRP rebar.
- Curing
- After the pultrusion process, the rebar undergoes further curing to ensure complete polymerization of the resin. This step enhances the mechanical properties and durability of the FRP rebar.
- Cutting and Finishing
- The cured FRP rebar is then cut to the desired lengths. Additional surface treatments may be applied to improve the bonding characteristics with concrete.
- Quality Control
- Quality control is a crucial part of the production line. The FRP rebar undergoes various tests to ensure it meets industry standards for strength, durability, and other performance criteria.
Advancements in FRP Rebar Production
The production technology for FRP rebar is continuously evolving. Some of the recent advancements include:
- Automated Production Lines: Automation has improved the efficiency and consistency of FRP rebar production.
- Enhanced Resin Formulations: New resin formulations offer improved bonding and higher resistance to environmental factors.
- Innovative Fiber Materials: The development of new fiber materials has enhanced the strength and performance of FRP rebar.
Conclusion
The FRP rebar production line is a sophisticated process that transforms raw materials into a high-performance product essential for modern construction. Its advantages over traditional steel rebar, such as corrosion resistance and high strength-to-weight ratio, make it an increasingly popular choice. As technology advances, the production process will continue to improve, offering even better performance and reliability in construction applications.
By understanding the production process and the benefits of FRP rebar, stakeholders in the construction industry can make informed decisions about incorporating this innovative material into their projects.